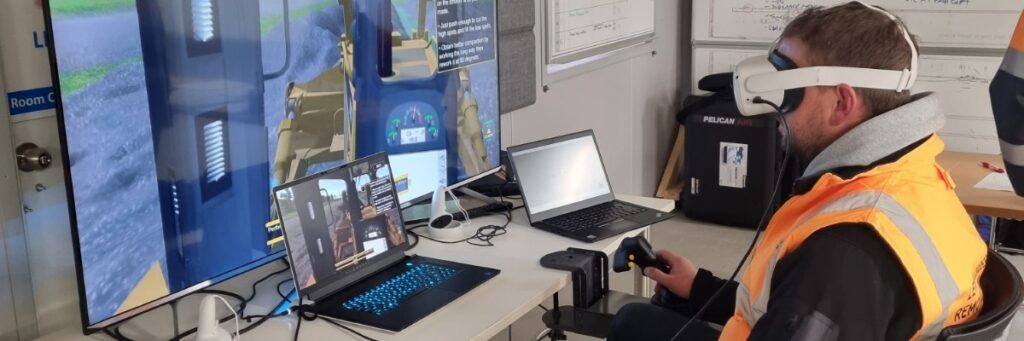
McConnell Dowell Employees Experience New Safety Program Featuring Cat® Simulators SimLite Systems with VR
For more than 60 years, McConnell Dowell has delivered innovative solutions for complex projects, ranging from remote resources to city infrastructure. The projects encompass building, civil, electrical, fabrication, marine, mechanical, pipelines, rail, tunnel and underground construction on two continents – Australia, New Zealand and Asia. Employee safety is a priority, from the plant (heavy equipment) operators to professional engineers to quality teams to all of the company’s employees and subcontractors.
In 2020, there were 194 fatal accidents and 120,000 serious injuries in Australian workplaces, according to Safe Work Australia’s “Work-related Traumatic Injury Fatalities, Australia 2020” report, with vehicle-related incidents being the leading cause of the fatalities. Industries such as construction and logistics disproportionately contributed to these statistics, making up approximately 68% of all fatalities. Despite industry best practices, such as exclusion zones, barriers, spotters, reversing cameras and training, these statistics have remained mostly constant for the past 20 years.
McConnell Dowell’s Australian Health and Safety Manager Greg Evangelakos explained that the company was seeking a training solution to help prevent incidents and fatalities for its more than 3,000 employees and 15,000 subcontractors who work across their projects. “What we found on our projects is that some employees and contractors lacked the understanding of plant (heavy equipment) and their blind spots,” said Evangelakos.
The company had been using various methods including safety instructions, training, induction, Safe Work Method Statements (SWMS), pre-starts and toolbox talks to ensure the safety of their employees and subcontractors. Evangelakos explained that although these methods were suitable, they were still looking to improve them.
“So, we challenged ourselves on how we could show or teach employees about interacting with plant (heavy equipment) and blind spots better. We needed a different way rather than us standing in front of 200 people, showing them a photo and explaining where the blind spots are,” explained Evangelakos.
The Health & Safety Team started exploring virtual reality (VR) as a solution.
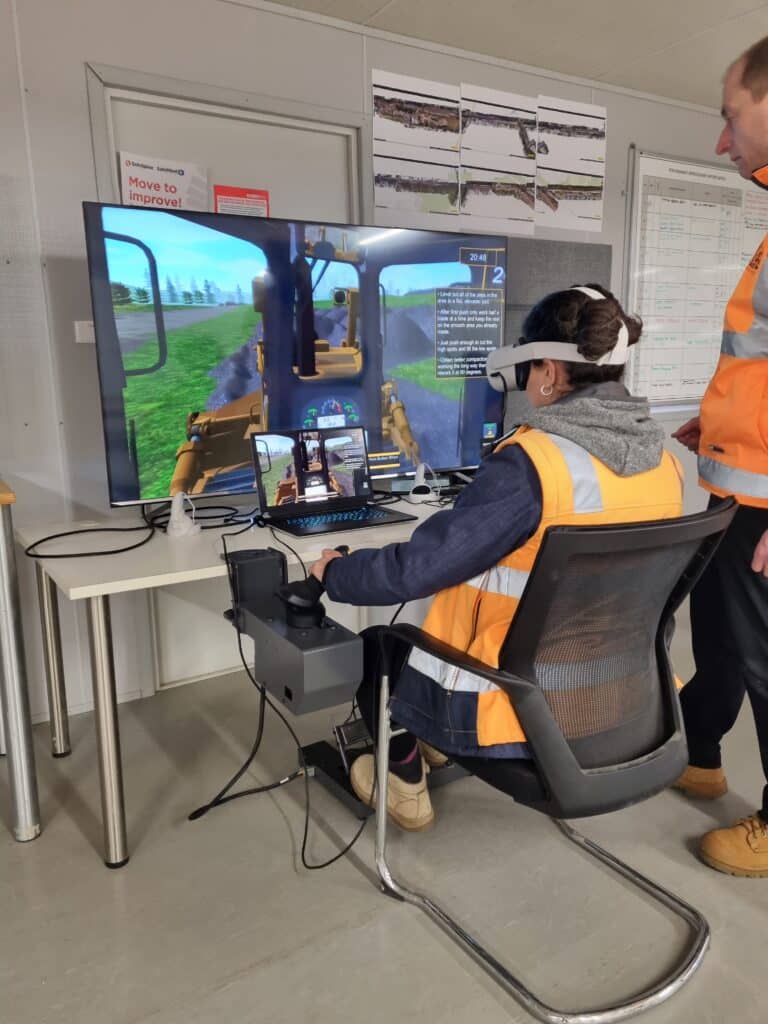
“We went down the virtual reality path with a developer to develop a program, but it didn’t work. It just wasn’t what we needed,” said Evangelakos. “Our next step was looking into virtual reality from an off-the-shelf product, so we contacted Cat® Simulators.”
The team knew Cat Simulators systems were used to train new and experienced operators how to operate heavy equipment effectively, but they needed a different type of training for their employees and subcontractors.
Evangelakos explained that they decided “to flip the simulator on its head” and use the simulators to help inexperienced employees from all disciplines gain a better perspective and awareness of heavy equipment and blind spots.
Rather than targeting experienced operators, the team focused on the broader workforce including quality team, engineers, surveyors and employees exposed to working around heavy equipment. “Basically, we targeted any employees we believed could be at risk were participants in our VR Simulation Plant Awareness Program,” said Evangelakos. “In the simulator, you get as close as possible to the real plant (heavy equipment) without being in real danger.”
VR Simulator Plant Awareness Program
Evangelakos continued, “Construction people and activities are inherently hands-on. We saw an opportunity with simulators to flip the education and understanding of the current industry best practice for people-plant interaction controls and make it even more hands-on.”
This was supported by the 70:20:10 model of learning and development. That model suggests that 70% of learning occurs through experience, followed by 20% through peer-to-peer relationships, and only a small portion, 10%, from coursework and training. Previously, employees had limited experiential learning. Now, their plant awareness and blind spot training is hands-on through total immersion because of VR, allowing them to experience firsthand the machine’s constraints and blind spot areas.
Project Safety Systems Coordinator Dru Morrish explained the program’s structure and use of the Cat Simulators SimLite Dozer and SimLite Excavator systems. “We use the simulators in a 10 – to 15-minute session with each participant. The objective is to increase the employees’ awareness of the plant (heavy equipment), how it operates, and the dangers associated with it,” said Morrish.
He explained, “The best way to do that, and the safest way, is through virtual reality because it’s as close as we can get to throwing them the keys and letting them get on a machine.”
Participants’ Tasks in the Program
When participants arrive, they are given an exercise sheet containing an aerial view diagram of either a dozer or excavator with a circle surrounding it. They must then draw the machine’s blind spots, based on their understanding of a typical operating environment and conditions. “We get them to mockup a spot, a wedge, a line or whatever they think the blind spots are,” explained Morrish.
After watching an instruction video on how to use either the dozer or excavator controls, they are ready to perform a pre-defined task for either machine. Participants using the Cat Simulators SimLite Dozer system find themselves in a pad leveling environment.
“We tell them to have a good look around, up, down, in and around. To make sure that they are familiar with their new cabin environment and surrounding worksite,” said Morrish.
The participants are then told to bulldoze the mounds into a level pad in front of them. “They may spend five to six minutes actually performing the operation,” explained Morrish. “After they are done, we give them the same exercise sheet they completed beforehand. And we say, now, based on your experience, can you draw the blind spots? Maybe your insight or awareness has increased after actually operating the machine. Maybe your thoughts are different now than before you started.”
Next, the participants are asked to recreate the worksite using little cardboard cutouts of the different scenery on the worksite, machines, trucks, any hard barriers, etc. The final task the participants must complete is a short survey.
“Most people have an overconfidence bias,” said Morrish. “They would answer, ‘Yeah, sure I would see someone if they were approaching me while I was operating the machine.’ Then I asked them the question, ‘How many trucks were around the worksite?’ It is not uncommon for participants to answer, ‘What? There was a truck?’”
“In the bulldozer example, there are actually three trucks in the scenario that are scattered around the pad,” explained Morrish. “They struggle to see any of the trucks, yet they claim they could see a person. Then they realize, ‘Well, maybe I wouldn’t see them. If I can’t see a truck, how would I have seen a person?’”
After participating in the VR Simulator Plant Awareness Program, participants not only have a better sense of the blind spots on the dozer and excavator, but they also appreciate the amount of concentration and skill that it takes to operate heavy equipment safely.
“For example, they learn about the momentum involved in the movement of a big machine. That it can be put in full reverse, but it doesn’t mean that it’s going to stop moving forward and instantaneously change direction,” explained Morrish. “So, the result is we find that the participants have a greater understanding of exactly what’s involved with operating plant (heavy equipment) and a greater empathy for the operator. They realize that it actually takes some skill and a large amount of concentration.”
“And the training breaks the stereotype that, unfortunately, plant operators can sometimes have where it’s just the guy who left school early and drives a machine for a living,” said Morrish. “From the outside, he’s a guy in a big glass fishbowl. I can see his boots and his hard hat, so he should be able to see me.”
“The simulator is a powerful tool for creating the world’s best operator,” noted Morrish. “But we’re not interested in that. We are getting the results we are looking for with the simulators in our program.”
Evangelakos concluded, “We are seeing a positive change using the simulator to change behaviors. That’s really evident. We’ve put close to 500 participants through the program, which lasts for 10 to 15 minutes but has a long-lasting impact on their respect for the plant and the operator. It does work.”