Avoid unnecessary downtime and extra depreciation by properly maintaining your Wheel Loader. Most important is to teach operators to complete a pre-operation walkaround inspection before every shift. Identifying issues before they become major problems can alleviate unplanned costs and missed production days.
Beyond the walkaround inspection and adhering to a regular maintenance schedule, follow these tips to help maintain your Wheel Loader.
- If the turbocharger fails during engine operation, severe damage to the turbocharger compressor wheel and the entire engine can result. Turbocharger bearing failures can cause large quantities of oil to enter the intake system and the exhaust system. Loss of engine oil can result in serious engine damage. Do not continue to operate the engine when a turbocharger bearing failure is accompanied by a significant loss of engine performance. Engine smoke and speeding up of the engine with no load are characteristics of a loss of engine performance.
- Tires should not be over or under inflated. Check the recommendations from the tire manufacturer. Look for missing tread and avoid running over large rocks and debris piles that could cause tire damage.
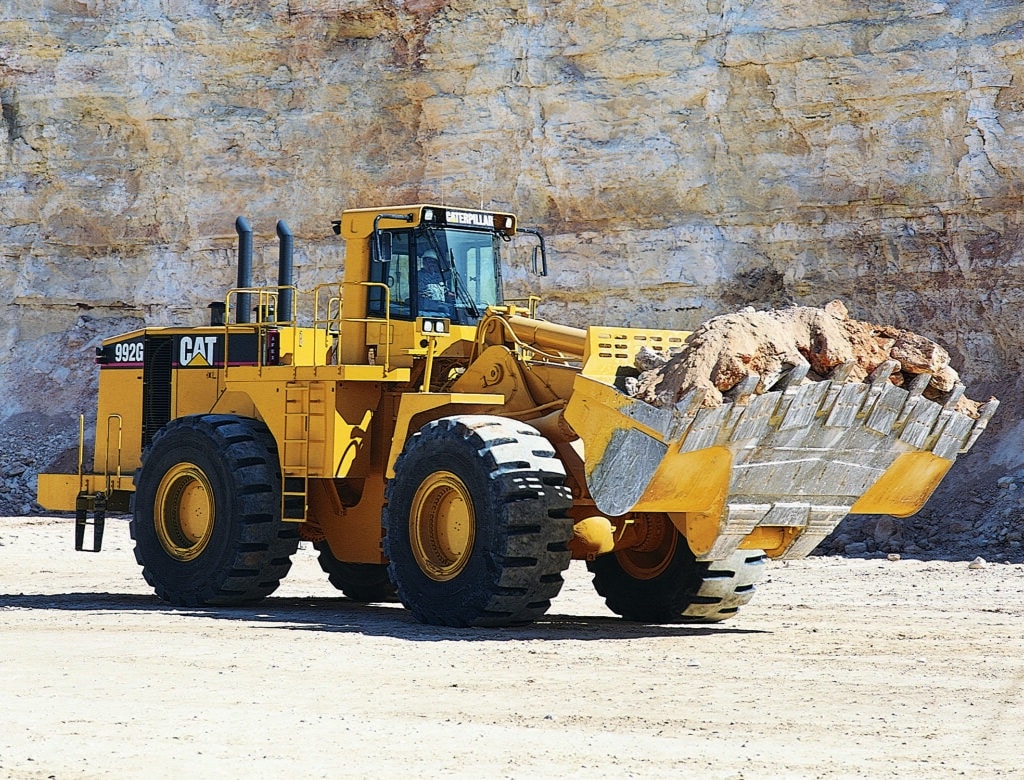
- Properly learning to use the brakes, including the parking brake, can help in maintaining the brake system over its expected life.
- Performing load and carry operations with a Small Wheel Loader usually means traveling at higher speeds for production purposes. Higher speeds will result in additional brake wear due to quickly slowing down the machine at either the loading or stockpile areas. Letting off the accelerator pedal earlier will allow the engine and transmission to assist in slowing down the machine, helping reduce brake wear. Using the auto shift feature can assist with this also.
- The impeller clutch/brake pedal should not be used for downhill braking on any size loader. Using the impeller clutch/brake pedal will disengage the engine from the power train. This action will increase the load on the service brakes, increasing the risk of significant wear and/or damage to the service brakes and final drives.
- Be sure to inspect the bucket cutting edges and end bits.
- If a missing tooth is noticed, get it replaced immediately to avoid further damage to the cutting edge.
- Never let a cutting edge wear to the base edge.
- Learn the load limits for the size of machine and do not overload the bucket. Overloading can cause tipping or spillage around the worksite. Running over spillage can cause tire damage.
- Avoid collisions with the truck when performing loading operations. Keep the work area platform level and clean to reduce spillage and help reduce the possibility of colliding with the side of the truck. When material spills, puddles or piles up, it could be run over and cause the machine to tip. Additionally, when the bucket is positioned high in the air or the machine is driven into a hole, the loader could become unstable and tip. The potential of collision damage, both to the loader and truck, can be very expensive.
- Dusty worksites are the norm in some areas of the world. Keep windows clean and clear. Keep in mind that dust can affect the radiator, filters, cooling systems, fans and other parts.