Heavy equipment tires are expensive and must be maintained to get the most life and value out of them. Operators should complete a walkaround inspection every day including checking for damage and wear on tires. Beyond the daily inspection, operators must know how to drive, brake, shift and maneuver equipment correctly. Training is the only way to ensure operators are using equipment correctly. Here are some examples of why heavy equipment tires may need to be replaced sooner than a planned life cycle.
Damage from Punctures & Cuts
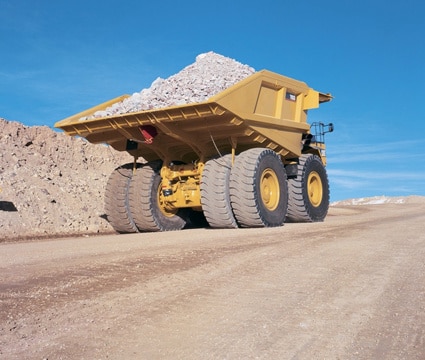
Construction sites often have nails, screws, glass, rebar, chunks of concrete and other types of debris that can lead to tire damage. Operators may be unable to avoid running over these objects, which makes an inspection even more important to catch tire damage before machines hit the worksite and possibly cause damage to another machine part.
Mine haul roads are culprits for tire damage when it comes to debris and potholes. Operators should avoid running over rocks, other types of spillages, large potholes or any pools of water that the bottom cannot be seen. It may be unclear how deep a crevice runs underneath the water. Support machines like dozers and graders can help keep haul roads clear for trucks and loading machines.
Under-Inflation or Over-Inflation
Be sure operators check the tire pressure regularly to make sure tires are not under or over-inflated. Tires can typically lose pressure every month possibly due to temperature changes or worn valve stems. An under-inflated tire can lead to tire failure. Under- and over-inflated tires can lead to diminished fuel efficiency. Follow the recommended guidelines set by manufacturers for tire pressure.
Mixed Tires
Follow the manufacturer’s recommended guidelines for tires. Do not mix tires, especially with different tread depths. Even a small difference in tread depth can lead to premature tire wear.
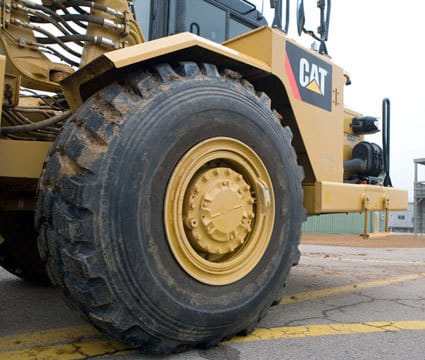
- Mixing tires from different manufacturers or adding new tires with worn tires is a mismatch.
- A mismatch can be caused by mixing different diameter tires, especially from one manufacturer to another. The smallest differences can cause additional wear.
- Differences in tire pressures among tires (even those that match in manufacturer and specifications) is considered a third type of mismatch. Check tire pressures regularly.
Tire Applications
Choose the right tire to match the job at hand. Premature wear or damage can be caused by using the wrong tires. Check and follow the manufacturers’ recommendations for tires. Everything from tread depth and strength to tire material and more can impact the life of the tire. For example, the type of tire needed for a Mining Truck is different than needed for an over-the-road semi-truck. Manufacturers will identify the right tires to use for the machine application.
Uneven Wear Patterns
Tires can be worn prematurely from running the same routes, braking, suspension wear, or from an overuse of torque (in addition to over- or under-inflation). Rotate tires regularly to even out tire wear patterns.
Tire Storage
Improper storage of tires can diminish their quality before they are ever installed on machines. Store tires in a dry environment, in moderate temperatures and away from direct sunlight. Never store tires in the same area as chemicals.
The operator is the key to avoiding debris contact, proper operation and inspecting assigned machines every day. Tire use affects maintenance costs and fuel economy. Operators must be correctly trained to best understand how to perform machine inspections, applications and techniques. Tire inspection is only one of the fault points covered in Cat® Simulators machine walkaround module. Additionally, each simulator focuses on applications developed with Cat expert operators that are specific to the machine. Step-by-step instructions and authentic Cat controls provide operators with effective hands-on training making the transition to the real machine seamless. Train operators on proper machine inspections, applications and good techniques—and reap the benefits.